La visita de Taiichi Ohno que desencadenó la lean excelencia de Rinnai
Desde que la visité por primera vez en 2011, me fascinó el nivel de excelencia lean Rinnai. Recientemente tuve el placer de entrevistar al Sr. Masao Kosugi, Director de Rinnai Corporation. Kosugi lleva en Rinnai desde que empezaron a estudiar el Sistema de Producción Toyota (TPS).
Siendo una empresa japonesa de primer orden, estoy seguro de que Rinnai practicaba un nivel bastante razonable de lean en 1979. Pero una visita de Taiichi Ohno, de Toyota, lo cambió todo.
“Taiichi Ohno visitó nuestra fábrica. Dijo que era horrible“, recordó Kosugi. Ohno también tuvo unas palabras bastante brutales para sus directivos. “Nos llamó a todos terribles gerentes y se fue”.
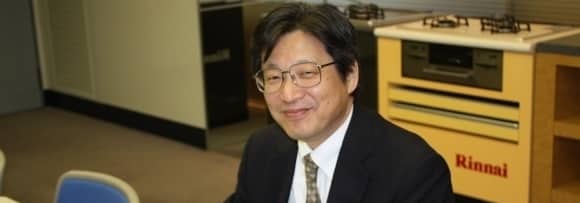
Ohno no centró su crítica en ningún área en particular, ni se centró en un tema determinado. “Todo fue malo”, dijo Kosugi. “La distancia recorrida por los operarios era excesiva, la cantidad de trabajo en curso era excesiva, la velocidad de producción era demasiado lenta, había elementos innecesarios desperdigados por todas partes…no había ni un solo aspecto bueno“.
Ohno estaba delante de muchos empleados de Rinnai cuando dirigió su spray a la dirección. Sin embargo, entonces el presidente Akito Naito* se dio cuenta de que lo que había señalado Ohno era bastante acertado. Desde ese momento, Naito quiso que Rinnai estudiara seriamente el Sistema de Producción Toyota. Muchos otros pensaron lo mismo tras presenciar la reacción de Ohno, y todos estuvieron de acuerdo en iniciar el viaje.
Rinnai pasó diez años desarrollando a sus empleados y las bases de la mejora antes de lanzar formalmente el Sistema de Producción Rinnai (RPS) en 1990. “Hay muchas empresas que se apresuran a implantar un sistema kanban y fracasan. Rinnai esperó diez años antes de introducir el kanban. De 1979 a 1989, practicamos el estilo Toyota de kaizen y eliminación de residuos. Estudiamos sólidamente los fundamentos”.
Mediante el kaizen y la eliminación de desperdicio, abordaron y eliminaron los problemas de cada uno de sus procesos uno por uno. “El resultado fue que cuando introdujimos el kanban, el nivel de cada uno de nuestros procesos era bastante alto. Así que no experimentamos ninguna interrupción cuando finalmente introdujimos el kanban y nuestro nuevo sistema de producción”, dijo Kosugi.
Sin embargo, Rinnai no ha desarrollado el Sistema de Producción Rinnai porque sí. Kosugi explicó: “Entendimos la importancia de las actividades de kaizen y de eliminación de desperdicio. Sin embargo, en aquella época no fabricábamos muchos tipos de productos. Planificábamos nuestra producción para fabricar un modelo en un solo día del mes. Hemos respondido suficientemente al mercado con este método. Estudiamos el camino de Toyota, pero no sentimos la necesidad de un sistema kanban o de un sistema de producción mixto en esa etapa”.
En la segunda mitad de la década de 1980, el mercado se volvió muy competitivo y se lanzó una avalancha de nuevos productos. “Una vez que empezamos a aumentar el número de modelos, algunos modelos tendrían demasiado stock, algunos modelos se quedarían sin stock, a pesar de que tenemos mucho stock en general. No teníamos el producto que queríamos, y no teníamos el producto que queríamos, por lo que la Temadel sistema de producción se intensificó.
Pensamos que si no cambiábamos nuestra forma de producir, crearíamos muchos problemas a nuestros clientes y el nivel de inventario general aumentaría. Así que tomamos la decisión de introducir un nuevo sistema de producción”.
Hubo algunas características clave en la forma en que Rinnai pasó esos diez años estudiando el TPS. En primer lugar, tenían un plan claro de etapas que seguían con disciplina. En segundo lugar, implicaron a todos los empleados en las actividades de mejora y mantenimiento de la producción. En tercer lugar, enviaron a algunos de sus propios empleados a Toyoda Gosei durante 12 meses para formarse en TPS. Y, por último, realizarían visitas periódicas a Aisin Seiki para aprender la teoría y la aplicación en el taller de sus esfuerzos de mejora.
El resultado es un espectacular ejemplo de excelencia en el trabajo ajustado. Naito, ahora en su role de Presidente, sigue desempeñando un role fundamental en el impulso de este esfuerzo. La planta de Oguchi fue, sin duda, la fábrica más visitada en el Shinka Management Lean Tour en Japón del pasado noviembre.
Taiichi Ohno no volvió a visitar la planta de Rinnai en Oguchi. Sin embargo, de alguna manera se enteró de la mejora realizada. “Todavía no tenía nada positivo que decir. Nunca iba a elogiarnos después de haber sido tan duro cuando nos visitó”, comentó Kosugi. “La gente de Toyota no suele elogiarnos. Pero a través de sus visitas a nuestra planta de Oguchi, cada año los comentarios positivos han ido aumentando poco a poco. Así que creemos que vamos en la dirección correcta”.
* El Sr. Akito Naito falleció tristemente en 2017. Su legado sigue siendo una inspiración para la dirección de Shinka.
Ben Sparrow es director de Shinka Management, una empresa de consultor leanque presta apoyo a clientes de más de 60 países para mejorar la productividad mediante las prácticas japonesas lean manufacturing. Su experiencia incluye ocho años con Japan Management Association Consultants (JMAC) transfiriendo conceptos y conocimientos japoneses de Lean Management y lean manufacturing a empresas de fuera de Japón de una amplia gama de sectores industriales.