The Taiichi Ohno Visit That Triggered Rinnai’s Lean Excellence
Since visiting for the first time in 2011, I have been fascinated with the level of lean excellence at Rinnai. I recently had the pleasure to interview Mr Masao Kosugi, Director of Rinnai Corporation. Kosugi has been at Rinnai since they first started studying the Toyota Production System (TPS).
Being a leading Japanese corporation, I am sure Rinnai were practicing a quite reasonable level of lean back in 1979. But a visit from Toyota’s Taiichi Ohno changed everything.
“Taiichi Ohno visited our factory. He said it was horrible,” Kosugi recalled. Ohno also had some quite brutal words for their senior management. “He called us all terrible managers, and left.”
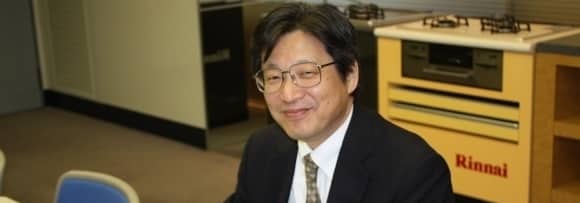
Ohno wasn’t focusing his criticism on any particular area, nor focusing on a certain theme. “It was all bad,” Kosugi said. “The distance travelled by operators was too far, the amount of work-in-progress was too much, the production speed was too slow, there were unnecessary items scattered all around…there was not one good aspect.”
Ohno was in front of many Rinnai employees when he directed his spray to management. However, then President Akito Naito* realized that what Ohno had pointed out was quite accurate. From that moment Naito wanted Rinnai to seriously study the Toyota Production System. Many others thought the same after witnessing Ohno’s reaction, and they all agreed to begin the journey.
Rinnai spent ten years developing their employees and improvement foundations before formally launching the Rinnai Production System (RPS) in 1990. “There are many companies that rush to implement a kanban system and fail. Rinnai waited ten years before introducing kanban. From 1979 to 1989, we practiced the Toyota style of kaizen and waste elimination. We solidly studied the fundamentals.”
Through kaizen and waste elimination they tackled and eliminated the issues in each of their processes one-by-one. “The result of this was that by the time we introduced kanban, the level of each one of our processes was quite high. So we did not experience any disruption when we finally introduced kanban and our new production system,” Kosugi said.
However, Rinnai did not develop the Rinnai Production System for the sake of doing so. Kosugi explained, “We understood the importance of kaizen and waste elimination activities. However at the time we did not produce many types of products. We would plan our production to produce one model all on one day of the month. We responded to the market sufficiently with this method. We studied the Toyota way, but we did not feel the necessity of a kanban system or a mixed production system at that stage.”
The latter half of the 1980s saw the market become very competitive and a flood of new products released. “Once we started increasing the number of models, some models would have too much stock, some models we would run out of stock, despite us having plenty of overall stock. We had the product that we didn’t want, and didn’t have the product that we wanted, so the production system issue was escalated.
We thought that if we didn’t change our way of producing, that we would create much trouble for our customers and the overall inventory level would increase. So we made the decision to introduce a new production system.”
There were some key characteristics in the way Rinnai spent those ten years studying TPS. Firstly, they had a clear plan of stages that they followed with discipline. Secondly, they involved all employees in improvement activities and production maintenance. Thirdly, they sent some of their own employees to Toyoda Gosei for 12 months to train in TPS. And finally, they would make regular visits to Aisin Seiki to learn the theory and shop floor application of their improvement efforts.
The result is a spectacular example of lean excellence. Naito, now in his role as Chairman, still plays an pivotal role in driving this effort. The Oguchi plant was certainly the most popular factory visited on the Shinka Management Lean Japan Tour last November.
Taiichi Ohno never made a second visit to Rinnai’s Oguchi plant. However, somehow he did hear about the improvement made. “He still did not have anything positive to say. He was never going to commend us after being so harsh when he visited,” Kosugi commented. “People from Toyota don’t generally praise us. But through their visits to our Oguchi plant, each year the positive comments have slowly increased. So we feel that we are heading in the right direction.”
* Mr Akito Naito sadly passed away in 2017. His legacy remains as an inspiration to Shinka Management.
Ben Sparrow is a Director of Shinka Management, a company of lean consultants supporting clients in over 60 countries to improve productivity through Japanese lean manufacturing practices. His experience includes eight years with Japan Management Association Consultants (JMAC) transferring Japanese lean management and lean manufacturing concepts and know-how to companies outside of Japan from a broad range of industry sectors.