OTRS Work Measurement Software
Kubota Corporation | Work element analysis speed improved by twofold! Transfer of the skills and know-how of veteran workers is also made easy using work measurement software
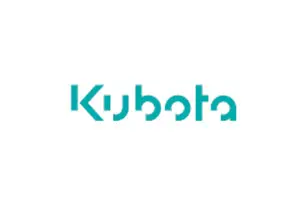

Industry: Manufacturing

Employees: 40,000

Revenue: See company website
Company: Kubota Corporation
Company website www.kubota.co.jp
Principal products manufactured in Utsunomiya Plant are rice transplanters and combine harvesters.
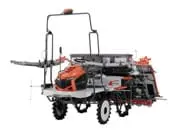
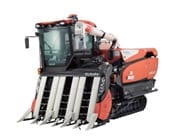
Issue
Analysis of five minutes of work used to take four hours and implementation of improvement measures took a long time
Outcome
OTRS10 work measurement software helped to speed up analysis work and implementation of improvement measures
Introduction background
Increasing the work analysis speed was imperative to enhance the shop floor capability
Utsunomiya Plant manufactures agricultural and farm machinery such as tractors, rice-transplanters and combine harvesters. The plant also functions as a “mother factory” for Kubota’s factories based in China and Thailand.
“Our sales in the Chinese market had been increasing steadily thanks to strong demand. However, the demand has now hit a peak. Since local manufacturers are also gaining competitiveness, producing high-quality products at lower cost is becoming increasingly important for us.” – Chihiro Ito
Toward this end, it was vital for the plant to analyze each work element in order to eliminate waste from their manufacturing processes. However, the conventional approach of using a stopwatch to time each element of work conducted on the shop floor and adding each data value into a PC required a long time. It used to take them nearly four hours just to analyze five minutes of work. As this was the case, making necessary improvements in a timely manner was quite difficult. To address this issue, Utsunomiya Plant decided to utilize a work measurement software tool to enhance their shop floor capability by emulating an example of the automotive industry which they regard as a benchmark.
“Various products are assembled on our mixed production line and the types of products made on the line change throughout the year depending on the season such as rice-transplanters in Spring and combine harvesters in Autumn. As we change process and operator layouts accordingly, it was crucial for us to improve our work analysis speed in order to address issues and implement improved solutions to achieve a positive outcome in a speedy manner.” – Chihiro Ito
Why OTRS was selected
Trial run started in consideration of OTRS’s superior functionality and versatility as a work measurement software tool
Utsunomiya Plant launched an IT tool utilization promotion project in the year 2013 to 2014. In search and test of effective IT solutions that would streamline their work element analysis tasks, they came across the work analysis and business optimization software, OTRS, at an IT trade show. After having checked and compared several similar work measurement software tools at the trade show, OTRS was deemed to be the best based on its user-friendliness.
“Operators working on our production lines are not that familiar with working on a PC. Since we wanted each section to conduct the complete task of work analysis and implementation of their work improvement solutions, it was important for us to have work measurement software that is intuitive and easy for everyone to use.”
– Chihiro Ito
What was appreciated highly was not only the superior work analysis functionality of the software but also other versatile functions such as creating standard work combination sheets and video manuals as this would allow them to create video manuals to capture the skills and know-how of veteran workers. The team purchased one software license key and started the trial run.
Introduction process
Four license keys purchased and utilized in all sections and lines
The work measurement software trial started with assembly line one as a model line where threshing machinery is assembled. Trial results were shared across the plant and other sections also tried the software. As the software received favorable reviews and many also wished to use it within their sections, the decision was made to purchase four licenses and introduce the software in full-scale across the plant. OTRS10 software is currently used extensively throughout the Utsunomiya plant.
“ Before the full-scale introduction, we held a software information session for all section chiefs. Following the software introduction, we became quite busy in following up with questions, but things settled down after a few months. Younger digital native workers learnt the software quickly in particular and this helped to create a positive culture in which they take a lead in implementing improvement measures for their shop floor. “ – Chihiro Ito
Introduction outcome
Analysis time reduced by half and transfer of veteran workers’ skills and know-how made easy through work measurement software
In the past, analysis of five minutes of work performed on the model line used to take as much as four hours to conduct. However, the OTRS software reduced the analysis work time by half.
On this model line, a total of 70 minutes worth of work was analyzed by OTRS in the FY 2017. Thanks to the software, they were able to reduce their work analysis time by 28 hours in total for the year. The increase in the work analysis speed meant more prompt implementation of improvement measures in the production lines. Though the condition of the lines change constantly throughout the year, issues are identified and addressed promptly within the same financial year without being carried over to the following year. This contributed greatly to the improvement of our productivity.
Another benefit brought by the software was making the transfer of retiring veteran workers’ skills and know-how easy and effective. The plant used to document and record video footage of the skills and know-how of veteran workers which they acquired over the years before their retirement so that they could be transferred to the next generation of workers. Thanks to OTRS, the recorded footage of their work can be broken down into small work elements and important tips and commentary can also be noted together with the footage, which made it a lot easier to utilize. Overall, the work measurement software proved to be a very effective tool in terms of skills and know-how transfer as well.
“The transfer of the skills and know-how required for manufacturing full custom products that are ordered only a few times a year was extremely difficult since not only the number of operators with the specific experience and skills are limited but also the training opportunities to produce such products on the shop floor are very scarce. However, through using work measurement software we can create video manuals that capture each element of work with detailed commentary. This proved to be extremely effective since operators can watch the necessary part of the production process repeatedly and learn the specific skills they require.” – Chihiro Ito
The next step
Expand the use of information through system integration
The next step for Utsunomiya Plant is to optimize the processes at all line and plant-wide levels in order to further improve their product quality and productivity. They are planning to establish a system where all the information collected in the plant is managed in an integrated manner by linking all the systems used within the plant. They are also looking into introducing the OTRS software to their other plants such as Hirakata Plant in Osaka as well as their overseas production sites in the future.
“ Demand for high quality products is expected to grow also in the Chinese market in the near future. With this in mind, it is vital for our products to have a competitive edge. Since the OTRS software can also be used in Chinese, it will also be an effective tool in our production sites in China in order to enhance our capability in the country for the time to come.” – Chihiro Ito
Customer Feedback
We are entering an era where effective ICT utilization is vital not only for product development but also product manufacturing
Kubota is a pioneer in mass production of global positioning system (GPS)-guided automated rice-transplanters with go-straight function. We have also rolled out KSAS (Kubota Smart Agri System) which provides a smart agricultural management support service based on big data utilization. Applications of such advanced ICT solutions are essential for future agriculture. We wish to strengthen the competitiveness of our products, services and manufacturing capability by accelerating the use of ICT.
Mr. Chihiro Ito
Manufacturing Department Division II, Utsunomiya Plant
OTRS is a time and motion analysis software product supported by Shinka Management, with an installation base of 6000 licenses spanning 20 countries.
For further information on OTRS10, or to request a demo or trial, see time study software.