OTRS Video Time Study Case Study
Yachiyo Industry Co., Ltd. | Promoting company-wide continuous improvement through Yachiyo System by taking the best out of OTRS and Value Stream Mapping
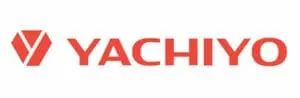

Industry: Manufacturing

Employees: 6,818+

Revenue: 166 billion yen
※1:Current at 31 Mar 2018 ※2:FY ending Mar 2018
Establishment: 27th August 1953
Address: 393 Kashiwabara, Sayama, Saitama
Business Description:
- Development and manufacturing of automobile functional parts (fuel tanks, sunroofs)
- Manufacturing of plastic and repair parts
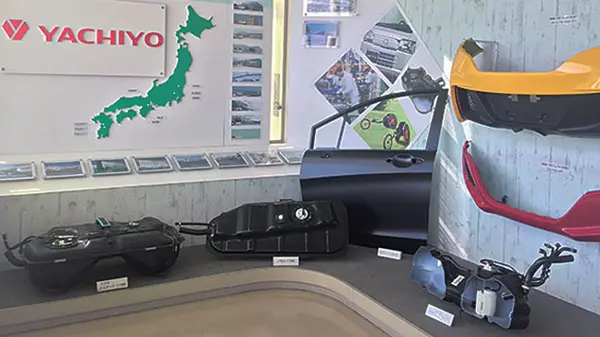
Issue
While the benefits of utilizing VSM and video were recognized, manual data collection and analysis had issues around efficiency and accuracy
Outcome
Video analysis that used to take two weeks to complete is finished in one day. Cost and time required to visit overseas production sites are reduced
Introduction Background (Issue)
There were issues around efficiency and accuracy when gathering data manually using a stop watch
Yachiyo Industry develops and manufactures automobile functional parts. The company has been making efforts to visualize their operational processes using value stream mapping (VSM) in order to achieve high-level work leveling to streamline their operations over the past three years. However, they had been unable to achieve the tangible results that they had hoped for. Given this situation, they decided to record the video of their works to supplement their VSM to analyze their work. As a result, they were able to expose their challenges and issues in great detail by reviewing their video recording.
However, as they started conducting time studies of their work elements manually using a stop watch in order to implement improvements, they soon realized how bothersome the time study work could be.
“After we selected the areas with issues based on our VSM and video recorded the work areas, we analyzed the video footage in great detail. As a result, we were able to identify the specific issues in the work areas such as operators were not moving their hands in a particular part of a process, materials were not flowing well from the previous process, tools were not placed close enough to the operators etc. Thanks to these pieces of information, we were able to identify the specific points for improvement.”
– Hidemasa Okubo
“Even when there is no more easily identifiable waste left in our processes, it is important for us to continue with eliminating waste to the level of 0.01 seconds. However, when we were conducting our time studies manually, it was taking too much of our time and the accuracy of the data we collected was questionable.” – Hidemasa Okubo
Why OTRS Work Analysis Software was selected
That our main customer was achieving good results with OTRS, and the software’s superior functionality and analytical capability played a decisive factor
One of the reasons the company decided to select and introduce OTRS was that one of their main customers, an automotive manufacturer had been utilizing OTRS for some time and had been achieving improvement effects. In addition, the software has widely been used by many other manufacturers in Japan.
“VSM is a process visualization tool derived from the Toyota Production System. For this reason, it did not align fully with our customer’s production system and culture. Since this was the case, we came up with our own Yachiyo System by using VSM to grasp overall issues and OTRS to scrutinize our problem areas “ – Hidemasa Okubo
Another reason was the superiority of OTRS functionality and analytical capability in comparison to other products. The intuitive user interface of OTRS also helps them to conduct their required analytical work more efficiently.
“OTRS allows us to modify our work elements with a click of a mouse and we can time each work element accurately to the level of 0.01 seconds. All the data we want such as time charts, net ratios, line efficiency etc. is created in a matter of seconds without us needing to put information in Excel sheets manually like we used to do before.” – Hidemasa Okubo
Introduction process
Seeing the effects of improvement not in one aspect of operation but as a whole
After analytical results and improvement suggestions based on OTRS video analysis were put forward, many of their colleagues wanted to know how they could also obtain such data as well as to have the data shared with them.
As the benefits of OTRS and its video analysis information started to gain a good reputation within their company, top management also became abletheir to recognize its benefits. As a result, the company began making efforts for improvements from both bottom-up and top-down directions.
“Our sales department told us that we can make improvements not only in one aspect of our operation but in the company as a whole. Since OTRS not only fits in well with VSM but also is used by our main customer, we thought it would work well for us. On top of this, what helped us to decide on OTRS was that we were able to get a good idea of its different functionalities and how they could assist us to make further improvements. We are now using OTRS to improve not just our shop floor but our entire company. “
– Hidemasa Okubo
Introduction outcome
OTRS provided new awareness and led the company to make steady improvements
By showing the graph of net ratio (the ratio of operation time over the entire production time) derived from OTRS to operators, they were able to distinguish the differences between value-adding work and waste. Mr Okubo was able to see the change in awareness amongst many operators as a result and they became more on board with making efforts for improvements.
“Previously, when I asked our operators on the shop floor how they could reduce the figures on the time charts, they used to respond with drastic answers such as they needed to change their tools and work procedures altogether or had to re-educate operators from scratch, and this type of thinking prevented them from moving forward. However, based on the analysis we conducted using OTRS, we were able to find out that the figures on our time charts could be reduced significantly by making simple adjustments such as modifying our material feeding methods and layouts.” – Hidemasa Okubo
Further to that, the company can now request their overseas production sites to record their operation and have the recorded footage sent to Japan. This allows them to analyze the operation at their overseas production sites and provides them feedback to implement improvements. As a result, the company was able to reduce the cost and time associated with their overseas site visits.
The next step
Aiming to achieve high-level work leveling by sharing data across the entire company
The company is working on making further operational improvements by utilizing OTRS and VSM. In order to assess the level of improvements implemented, they focus on a simple figure derived from a formula of “value-adding time (operation time)/lead time” based on the numbers obtained from the detailed OTRS analysis. When the figure increases from 1/2000 to 1/1800 for example, they can confirm that they were able to make improvements in their operations.
“In the past, we were frequently experiencing the issue of not being able to assess our improvements properly. Even when we successfully reduced our labor cost, there were times when our total cost increased due to increase in logistic cost or product defective rate. However, the figures derived from this simple formula can effectively indicate how much waste we have eliminated from our operation. This is certainly helping us to increase our production efficiency. Operators on the shop floor also find this useful as it is simple and easy for them to understand.“ – Hidemasa Okubo
“What we want to do next is to share our OTRS data with our colleagues in other departments such as Production Technology and Development departments. Our company is manufacturing the same products across all our global sites. However, depending on where they are manufactured and who is in charge, there are variations in our production approach and our product quality at the moment. To move forward, we want to improve this situation and achieve high-level work leveling across our global sites.“ – Hidemasa Okubo
Moreover, what is recorded on video and the figures derived from OTRS won’t lie. Top management of the company have been well convinced by this evidence and the unique Yachiyo System they have developed has steadily been gaining good recognition within the company.
Customer Feedback
To make the best out of OTRS, users must keep working with the software
While OTRS is an intuitive, easy-to-operate software, it is not a magical tool that anyone can pick up and start making the full use of in an instant. It requires a certain level of training in order to have a good command of the software. I started using OTRS six months ago. Over the past six months, I spent week after week to get myself better at the software. I know I can get even better at it. Firstly, I want to make sure I gain a full command of OTRS to get the best out of it so that I can spread the benefits of the software across our company.
Mr Hidemasa Okubo
Plant Manager, Production Department, Suzuka Plant
OTRS is a time and motion analysis software product supported by Shinka Management, with an installation base of 6000 licenses spanning 20 countries.
For further information, or to request a demo or trial, see OTRS10 time study software or view information on the companion mobile time study app.