Lean Photography – A Young Professional’s Lean Business Transformation
Is lean management mainly for the manufacturing industry and for big businesses? The answer is no. Lean management and Toyota Production System principles offer excellent and practical process management ideas and tools for anyone who wishes to improve their productivity and operational efficiency.
However, if this the case, where can we find some practical examples of these tools being applied outside of the manufacturing industry and in small businesses?
In this article on lean photography, I would like to share an inspiring story of a young professional photographer’s lean business transformation and how he has refined his operations through the application of TPS methods to achieve considerable benefits. His story gives us a great insight into how even creative industries, such as a photography business can adopt lean principles to improve their processes, customer satisfaction and ultimately profits.
Background Story
Juan Van Staden is a young professional photographer and videographer based in Adelaide, South Australia, who produces some of the most amazing high-quality photographs and videos as featured on our website. Shinka Management has been lucky to have him on board as our corporate photographer since 2014 and has had him join us on the majority of our Lean Japan Tours over the years.
What we appreciate about him is not just his talent, skills and highly approachable manner but also his constant aspiration for continuous improvement or kaizen. As our dedicated Lean Japan Tour photographer, Juan has had abundant first-hand exposure to lean methodologies not to mention many fine examples of TPS applications at work in Japan. Having had these beneficial experiences whenever he was on tour, it didn’t take long before Juan was convinced that TPS was something that he could also apply to improve his own photography business. Ever since this revelation, he has been translating his new learnings into actions and he has made several cost-effective positive changes in the way he runs his business.
As with all kaizen efforts, Juan is still continuing to polish up his processes further. Below I have showcased some of the interesting examples of his TPS applications that he has made in his photography business to date.
Importance of Waste Identification and Process Standardization
As a busy photographer, Juan spends much of his time on photo shoot sessions outside of his own studio. When he is active out on location, he needs to set up and pack away his professional equipment such as tripods, light modifiers, backgrounds etc. This is something he has to do every time before and after photo shoots. According to Juan, he used to spend about one hour to do this. But, through looking at his procedure through a TPS lens, and adapting concepts from SMED (Single Minute Exchange of Die) and rapid changeover practices, he realized that the time he spends for his setup and pack up is essentially all waste as this doesn’t add any value to what he does as a photographer. Arguably, the only value-added work (also known as net work) that takes place during his photo shoots occurs only when he releases the shutter of his camera – the rest is all waste. However, under the current situation, the equipment set up/pack away procedure is a necessary process in order for him to perform his work.
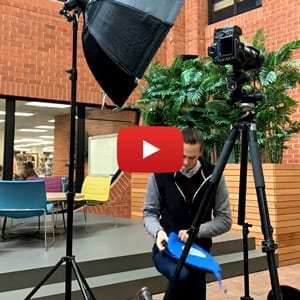
Video: Juan’s pack away procedure
So, Juan decided to divide this into necessary and unnecessary waste. He broke down this routine process into small elements and conducted a time study to analyze each element of work to identify unnecessary waste. In addition, since the entire set up/pack up process always involves the same steps, he created standard work around this based on his time study results.
He came up with a much-improved low-impact procedure while eliminating all the unnecessary wasteful movements he identified. Juan now applies this standard work routine every time he needs to prepare and pack away his equipment for a photo shoot session.
Thanks to such efforts, the results he achieved have been remarkable. Juan has so far been able to reduce the set up/pack away time by half compared to when he had no standard around these processes. This impressive outcome not only benefited him but also was welcomed by his regular clients as the time he required on their site was also reduced.
The clients Juan works with and the images he creates during each session are different every time, but the process required for him to take photos every time is typically the same. What Juan did here is a fine example of identifying repetitive work even within the creative industry sector and applying a TPS approach to streamline these processes.
Simple but Effective Kaizen Solutions
Talking about waste elimination and work standardization, Juan also standardized how he packs his gear. He clarified what pieces of equipment he usually takes to his photo shoots, how many of those items he needs to take and how and where they are packed in his carry bags. Juan says that this seemingly very simple approach inspired by lean practices such as 5S and visual management has helped him greatly, not only to get himself ready quicker but also to prevent him from leaving necessary items behind at home or at his client’s location after the session. No more going back home or follow up phone calls and emails to his clients and wasting time to fetch the items he left behind.
Juan has also thought about how he could reduce the volume of his luggage by packing his professional equipment in a more planned and compact way, which has enabled him to reduce the physical burden of carrying previously a number of bags on his shoulders, reducing the load down to one wheeled bag. With an increasing need to travel by plane, Juan certainly appreciates the benefit of packing and traveling smarter.
You could see how Juan goes through his standard packing process in the video included above. Juan found it much easier and faster to go through the process when his bags are placed in a small circle around him and pack up all his equipment while he is sitting on his knees rather than getting up and down so many times.
As these examples highlight, Juan is now seeing everything from a kaizen perspective. It is so refreshing to see how Juan always looks for things to improve and applies kaizen to reach better solutions!
Another inspirational application of lean methodology in Juan’s operations is how he adopted Toyota’s heijunka (leveled production) concept and the use of a heijunka box into his editing work to streamline his operational flow. As the volume of his work started to increase, Juan needed an effective photo editing planning and management system in place to keep up with a varying and growing demand. To address such challenges, Juan successfully systematized his editing process by incorporating the idea of Toyota’s heijunka box tool to streamline his photo editing process.
Operation Planning, Heijunka Box and Kanban
For those who are not familiar with the concept, heijunka is a Japanese term that is often translated as “production leveling” in the context of lean production. This is a production planning technique used to achieve smoother operational flow by reducing unevenness (mura) both in the mix and quantity of products being made in order to efficiently meet customer demands while eliminating waste (muda) and minimizing overburden (muri) in the production system. Mura, muda and muri are collectively known as the three enemies of lean production that should be avoided.
While heijunka is the leveling or smoothing of production, the heijunka box is a visual scheduling tool used to achieve the aim of heijunka. With a predetermined interval of work and the use of work instruction kanban cards, this tool allows production to be signaled in a leveled manner.
Having seen an example of a heijunka box in use within one of Toyota’s automotive parts suppliers, Suzaki Industries, during a Shinka Management Lean Japan Tour, Juan created his own heijunka box to address his needs. Thanks to this tool, not only can Juan maintain progress on his photo editing work at a constant rate, but also the tool helps him to detect and control abnormalities in the editing process. Since Juan promises his clients a two-workday turn-around for most of the jobs he accepts, he has to deal with the pressure of a varying volume of work depending on the number of photo shoot sessions he conducts in a given time. However, the heijunka box visual scheduling tool makes it possible for him to keep up with this pressure and to make sure his clients’ delivery time requirements are fulfilled. Juan says that this tool works particularly well now that he has an assistant working for him to help out his editing work on every alternate weekday. So, how does this really work for Juan and his assistant?
How Juan’s Heijunka Box Works
As you can see in Picture 1, Juan created a heijunka box divided into six sections with each one dedicated for Monday to Friday and the following week. Each day of the week is then further divided into seven slots based on one-hour time intervals. Work instruction kanban cards and a workstation were also created to be used together with the heijunka box (see Picture 2).
Picture 1 – Heijunka Box
Picture 2 – Work Instruction Kanban
When Juan returns back to his office after a photo shoot session, he places his memory cards in the “IMPORT” tray on the left side of his work station and prepares a work instruction kanban card for each editing job by filling out the information necessary for his assistant to perform the work, such as photo shoot location, client name, expected editing time, price for the editing work, etc.
With regard to the expected editing time, Juan conducted time studies around his editing process prior to the introduction of the system to find out how much editing time one photo shoot job would require depending on the type of work (e.g. commercial portraits, event photos etc.), the number of photos taken, and so on. He uses his time study results as a guide to estimate the expected editing time for each job which he writes down on a kanban card. Following this, Juan places the kanban card for each editing job into appropriate slot of the heijunka box in consideration of the client’s priorities, other editing work, etc., and in doing so creates a production schedule for his assistant.
When his assistant comes into the office, she imports the images from Juan’s memory cards onto his computer according to an established filing system and takes out the new kanban card from the heijunka box, placing it on the workstation to start the required editing work.
In the case of Picture 1, for example, Juan’s assistant knows that she needs to start the editing work placed in Monday’s 12pm slot and has to complete it within eight hours by Tuesday 2 pm. She also knows that she has one more job waiting for her to complete by 5pm on the same Tuesday. As you can see, each kanban card also has the section to track the progress of each editing stage such as “Lr (Lightroom)” and “Ps (Photoshop)” which are crossed off by using an erasable marker as she makes progress and completes each step of the editing work.
Upon the completion of the editing work, she removes the kanban card from the workstation and puts the memory card into the “IMPORTED” tray of the right side of the workstation so that Juan can take the memory cards from the tray for his new photo shoot.
What Juan has implemented here is a basic take on the heijunka concept. However, this system is tweaked to serve for his purpose and works effectively as his editing work volume is evened out and the work processing rate can remain fairly constant. In addition, where there is an abnormality such as a delay or some kind of disruption in the editing process, Juan’s attention is drawn to this when he returns to his office by checking the status of the kanban cards in the heijunka box as well as on the workstation. If the editing job he allocated hasn’t been progressing or completed according to the plan (i.e. kanban cards are not removed from the heijunka box or progress tracking sections on kanban cards are not crossed off as planned), he can step in by working at night, for example, to catch up with the delay by the next morning. In the worst-case scenario, he can discuss the issue with his client in advance rather than realizing on the day of delivery that there is a delay. What is more, he can investigate the reason for the delay and can address the root cause of the problem with his assistant so that the same problem doesn’t reoccur.
Incentive for Working Smarter
Another ingenious point about Juan’s system is that it gives a good incentive for his assistant to work smarter. In order to provide her financial stability, Juan guarantees his assistant a fixed base salary for the minimum hours required for her to be in the office regardless of the editing work to be performed as she is paid to take care of other office/administrative work since Juan has ongoing regular photo shoots throughout the year. On the days when there is editing work for her to fulfill, the dollar amount indicated on each kanban card is guaranteed as an additional payment made to her as long as she can finish the work according to the schedule set by the heijunka box system. Since the amount of pay is pre-determined for each work, if she works faster and can finish the work in advance, her hourly rate for her editing increases. Likewise, if she takes more time, her hourly rate drops accordingly. This helps Juan’s assistant to be self-aware and motivates her to continually improve her editing processes by making them more efficient.
Juan says that he cannot stress enough the importance of giving new ideas a try and working through trial and error to come up with efficient and refined operational processes as this not only helps to increase his revenue potential but also his clients’ satisfaction level as well.
Moving Forward
As his reputation spreads and demand for his service increases, Juan recognizes the need of expanding the number of assistants and sub-contractors in his team to move forward. He is currently looking into how he can continue to guarantee the quality of his work when more people are involved in his creative processes. To this end, he is considering to implement a number of new ideas including creating a skills matrix chart to assess and coach the required skills, abilities, knowledge, and strength of those who would be working under him.
Juan said that he was always interested in improvement but didn’t necessarily know how to go about it. But, the first-hand exposure to lean principles in Japan has changed how Juan sees things around him and has given him a clarity, good foundation and the practical means to approach many of the issues and challenges he faces in his day-to-day business operations.
Conclusion
Eri Dennis is a Consultant of Shinka Management, a lean training and consulting firm with clients in over 60 countries. Eri is a regular leader of the Shinka Management Lean Japan Tour. Eri graduated with a Master of Arts in Japanese Interpreting and Translation from the University of Queensland and is NAATI accredited as a Professional Level Interpreter and Professional Level Translator.