Caso di Studio del Software di Ottimizzazione del Lavoro OTRS
Toyota Boshoku Corporation | Utilizzo di video per condividere i punti che richiedono un miglioramento
e aumento della produttività di circa il 25% con il software di ottimizzazione del lavoro OTRS10

Industria: Produzione

Dipendenti: 41,409

Ricavi: 1,4 trilioni di yen
* Consolidato (esercizio 2017)
Fondazione: 1918
Indirizzo: 1-1 Toyodacho, Kariya, Aichi 448-8651
Descrizione dell’attività:
- Attività di fornitore di sistemi per interni e di produzione e vendita di prodotti per interni
- Produzione e vendita di filtri per autoveicoli e parti di ricambio per motori
- Produzione e vendita di altri componenti per automobili
- Produzione e vendita di prodotti tessili
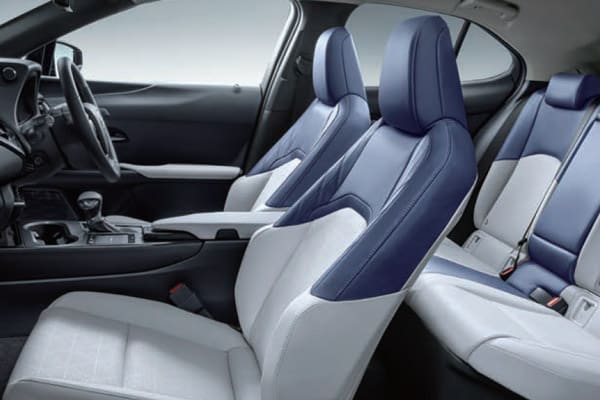
Problema
Variazione del lavoro a seconda di chi lo svolge e incapacità di aumentare la produttività
Risultato
La produttività è aumentata di circa il 25% e il piano di produzione è stato raggiunto grazie all’uso di un software di ottimizzazione del lavoro.
Introduzione Contesto (problema)
Non c’era alcuna standardizzazione dei documenti aziendali cartacei o del lavoro in loco.
Il Gruppo Toyota promuove la standardizzazione del lavoro nei siti di produzione sulla base di un motto che sottolinea che non ci possono essere miglioramenti senza standardizzazione. Alla Toyota Boshoku Corporation, un’azienda del Gruppo Toyota, i tre fogli di standardizzazione fondamentali (foglio di capacità produttiva, tabella di combinazione del lavoro standardizzata e tabella di lavoro standardizzata) e altri documenti venivano gestiti su carta. Tuttavia, la quantità di documenti scritti da ciascuno (il livello di dettaglio) variava e il lavoro variava a seconda del lavoratore che lo svolgeva. Sebbene i depuratori d’aria e altri prodotti importanti siano stati migliorati di un certo livello nel corso del tempo, miglioramenti simili non erano evidenti per le linee di produzione appena avviate. C’erano anche problemi con l’accuratezza del tempo standard inizialmente determinato, i numeri differivano a seconda del luogo e si verificavano tempi di inattività.
Ciò ha comportato problemi che devono essere affrontati prima di poter apportare miglioramenti, come ad esempio la necessità di rivedere il tempo standard misurandolo nuovamente con un cronometro. Quando il signor Numa, che in precedenza lavorava per Toyota Motor, è diventato il nuovo presidente di Toyota Boshoku, ha sollevato i problemi del sito di produzione di cui sopra e ha avviato un progetto per apportare miglioramenti e risolvere i problemi.
“Quando il Presidente Numa ha visto che i documenti aziendali dello stabilimento di Kariya non erano stati standardizzati, ha subito sottolineato che non era possibile che il nostro lavoro fosse standardizzato e che avremmo dovuto fermarci, fare un esame approfondito del nostro lavoro attuale e ripartire da lì.” – Takashi Sato, Unità Promozione Globale dello Stabilimento di Kariya, Stabilimento di Kariya
Perché è stato scelto il software di ottimizzazione del lavoro OTRS
Il software per l’ottimizzazione del lavoro OTRS10 è stato selezionato in base a una prospettiva top-down, data la sua storia di utilizzo per lo sviluppo
Il Presidente Numa ha suggerito il software di ottimizzazione del lavoro OTRS come strumento per analizzare la situazione lavorativa. La decisione di introdurre l’ultima versione di OTRS nello stabilimento in cui lavora il sig. Sato è stata presa in gran parte grazie ai risultati ottenuti dal software in oltre 20 anni di storia.
“Con i tipici software di editing video, tutto ciò che si può fare è registrare un video e guardarlo. Tuttavia, con OTRS10 possiamo utilizzare i dati video registrati per eseguire un’analisi operativa dettagliata di ogni elemento del lavoro. Credo che questo renda il software di ottimizzazione del lavoro OTRS10 lo strumento migliore per determinare facilmente come standardizzare correttamente il lavoro”. – Takashi Sato
Processo di introduzione
Oltre sei mesi di collaborazione per garantire che il software di ottimizzazione del lavoro potesse essere utilizzato sul posto.
Dopo l’introduzione di OTRS nel febbraio 2017, il sig. Sato ha trascorso più di un anno e mezzo fino a ottobre valutando attentamente le modalità di utilizzo del software, compresi aspetti quali lo sviluppo di standard per i documenti di lavoro e aziendali, la raccolta dei dati e la creazione di database. Ha anche suggerito a Broadleaf, il produttore, degli aggiornamenti per migliorare l’usabilità del software per vari tipi di produzione e ha chiesto loro di implementare gli aggiornamenti, gettando così le basi per un utilizzo efficace del sistema.
“Ad esempio, su una delle nostre linee c’era un lavoro accidentale e irregolare che si verificava una volta ogni cinque cicli e che comportava dei tempi di inattività. All’inizio OTRS non era in grado di tenere conto di questo lavoro accidentale, ma Broadleaf ha reso possibile questa operazione non appena l’ho proposta. Siamo quindi riusciti a digitalizzare i tempi di inattività che non potevano essere espressi con i tradizionali documenti aziendali scritti a mano e a standardizzare il nostro lavoro sulla base dei dati analizzati”. – Takashi Sato
Risultato dell’introduzione
OTRS10 ha permesso di verificare chi ha lavorato più velocemente e di aumentare la produttività di circa il 25%.
L’azienda aveva problemi ad aumentare la produttività del nuovo motore con ingranaggi, ma si trovava a dover produrre un numero di unità che superava la sua capacità produttiva del momento. Era necessario un rapido miglioramento, quindi il capo responsabile ha dato immediatamente il suo consenso e hanno iniziato a filmare il lavoro svolto dai dipendenti giorno e notte. Utilizzando OTRS10 per eseguire un’analisi dettagliata di ogni elemento di lavoro, hanno scoperto che il lavoro variava a seconda di chi lo svolgeva.
Grazie a un’analisi comparativa dettagliata dei dati, ora possono capire chi svolgeva il lavoro più velocemente per ogni elemento. La visione dei video da parte di tutti ha permesso di spiegare modi specifici di usare le mani, che prima erano difficili da insegnare con i tradizionali manuali cartacei. I lavoratori hanno anche elaborato diversi piani di miglioramento e Toyota Boshoku ha ottenuto un aumento della produttività di circa il 25%.
“Grazie a un notevole aumento della produttività, abbiamo iniziato a capire che potevamo davvero realizzare il nostro piano. Inoltre, la cosa che mi ha reso più felice di tutte è stata quando il capo cantiere, un uomo orgoglioso della sua abilità artigianale, ha detto: “Grazie per aver introdotto uno strumento così bello”. Temevo che l’introduzione dell’OTRS10 potesse essere una seccatura per le persone che lavorano sul posto, ma tutti sono stati davvero collaborativi nel darsi consigli a vicenda, il che ha portato a un miglioramento del lavoro di squadra. Ad essere sincero, mi sono sentito molto sollevato”. – Takashi Sato
Dopo un periodo di preparazione così intenso, è finalmente iniziata l’attività OTRS su larga scala nella linea di produzione del nuovo prodotto “Motore con ingranaggio” (prodotto unitario per la regolazione della posizione del sedile).
Il prossimo passo
Promuovere l’uso di OTRS10 in tutta l’azienda e puntare a miglioramenti costanti.
Ora che i vantaggi dell’utilizzo di OTRS sono diventati evidenti, il signor Sato ha assunto un nuovo ruolo basato sul successo dell’applicazione di OTRS al motore con ingranaggi: espandere l’uso di OTRS10 ad altre linee di produzione di Kariya Plant e a stabilimenti sia all’interno che all’esterno del Giappone.
“Mentre raccolgo i dati nello stabilimento di Kariya e li compilo in un database, spero di introdurre il sistema in altre linee e fabbriche e di insegnare ad altre persone come usarlo. Sono già in corso iniziative analoghe presso i nostri stabilimenti in Thailandia e la prossima settimana mi recherò nuovamente in visita per fornire indicazioni. Dato che i lavoratori provengono da ambienti e paesi diversi, credo che l’utilizzo del software di ottimizzazione del lavoro OTRS per fornire istruzioni visive attraverso i dati sia più adatto rispetto all’approccio convenzionale che dipende dall’intuizione di un lavoratore basata su una lunga esperienza. Sarebbe bello se questo portasse a un aumento delle competenze dei lavoratori (sviluppo di più competenze)”. – Takashi Sato
Feedback dei clienti
Grazie alla possibilità di controllare i video di lavoro da un punto di vista esterno, abbiamo scoperto nuove cose.
Il mio motto è quello di mettere subito in pratica tutto ciò che è utile, quindi mi sforzo di apportare miglioramenti su base giornaliera ed ero interessato a utilizzare i video di OTRS anche per l’analisi dei dati di lavoro. Quando ho mostrato i video registrati ai lavoratori, la prospettiva di terzi ha permesso loro di vedere il lavoro da migliorare e quello da utilizzare come esempio. Dandoci suggerimenti reciproci, scambiandoci attivamente opinioni e adottando azioni simili, siamo riusciti a velocizzare il nostro lavoro. In seguito, la condivisione del buon lavoro con tutti come nostro standard e la padronanza dello stesso hanno aumentato la motivazione di tutti i lavoratori. Credo che i video registrati possano essere utilizzati anche come strumento efficace per la formazione dei nuovi lavoratori.
Masafuyu Ito
Chief Leader, Unit 4 Sec., Oil Unit Parts Manufacturing Dept., Manufacturing Div., Kariya Plant, Toyota Boshoku Corporation
OTRS è un prodotto software per l’analisi del tempo e del movimento supportato da consulenti lean Shinka Management, con una base di installazione di 6000 licenze in 20 paesi.
Per ulteriori informazioni o per richiedere una demo o una prova, vedi il software di analisi del tempo OTRS10.