Our lean consulting team caters for your unique, individual circumstances. Our lean consultants support you in developing and deploying processes, systems and leadership to address the challenges that you experience in your operating environment and to achieve your vision and goals for your company’s future.
Your people need not be lean experts to apply the right tools and develop the correct mindset around problem solving. We work with your corporate culture and language, and provide a bespoke approach to establishing business excellence appropriate to your people and priorities.
Although the tools we work with are simple, effective and sustainable, implementation is the challenge. This is where our senior lean consultants and our lean journey framework, the Shinka Management Way, add value.
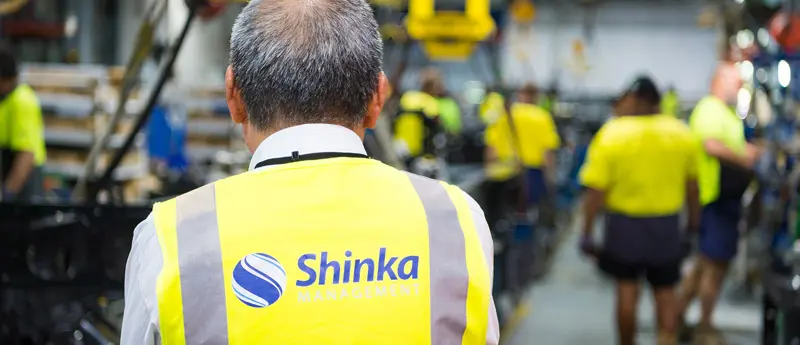
Our Lean Consulting Team
Shinka Management’s lean consultants understand the true essence of lean. Our experience in lean consulting originates directly from the home of lean manufacturing – Japan.
Our approach is one that has not been affected through misinterpretation in the West. It is a proven methodology that has resulted in world-class operational excellence in thousands of organisations. Moreover, our lean consultants have extensive global experience in the application of lean manufacturing outside of Japan and understand the original language and culture in which it was developed.
Shinka Management has the ability to provide cross-functional teams of lean consultants for the full support of our clients. Our team of lean management consultants, including veteran Toyota Japan Factory Managers and Japan-trained senior consultants, have decades of experience of applying lean management innovation across industry, government and not-for-profit organizations.
We are experienced at understanding our clients’ true circumstances and pressing problems. We provide coaching and support to guide your team on its lean journey, and provide direct facilitation and project management for your more pressing and immediate problems.
For further information, contact us via the inquiry form below to discuss how our team can support your lean journey.
What do Lean Consultants do?
Lean consultants are experts in lean management, a method aimed at eliminating waste and enhancing efficiency in business processes. They identify areas of waste, devise strategies to reduce it, and implement lean principles such as Just-In-Time production and continuous improvement. Lean consultants also provide training to employees, manage changes in processes and workflows, and establish key performance indicators to measure success.
At Shinka Management, our ultimate goal is to help our clients implement and sustain a culture of continuous improvement based on lean management principles.
Case Study | Escorial’s Lean Journey
Faced with rising costs and increasing market demands, Argentine white goods manufacturer Escorial partnered with Shinka Management to embark on a lean transformation across its two production plants.
The initiative began with a lean training program in Japan, followed by an 18-month implementation support program led by Shinka Management’s senior consultant Daniel Andreu.
The result? Improved productivity, greater engagement across the workforce, and the foundation of a continuous improvement culture embedded within daily operations.
This case highlights the impact of applying Japanese lean culture in a Latin American manufacturing context.
⇒ Explore the full case study to see how Shinka Management’s lean implementation approach helped Escorial boost productivity and drive lasting operational change
It’s truly inspiring to witness the active participation of our employees in the PIME 4.0 kaizen suggestion scheme. Their engagement reflects how deeply the culture of continuous improvement is taking root across the organization. The steady increase in submitted suggestions continually challenges us—not only in terms of managing them effectively, but also in ensuring we allocate the necessary resources for their implementation.
Designing a recognition system for implemented ideas has been a particularly rewarding aspect. This system, which tracks the maturity of the EPS, plays a vital role in sustaining motivation, allowing everyone to clearly see the tangible benefits of their contributions. We’ve seen how employees are now integrating the generation of improvement ideas into their daily routines, with the added satisfaction of seeing these ideas put into practice in their own work environments. This sense of ownership brings great pride—both in the value they add and in knowing their voices are heard and their input leads to real change.
Since the program’s inception, our Continuous Improvement Team has grown and evolved significantly, and Shinka Management’s guidance has been instrumental in this journey. We are confident that we’re on the right path and must continue progressing—strengthening our culture of continuous improvement through the development of every person who is part of Escorial.
Read more about the support provide by Shinka Management at Escorial Argentina:
Case Study: Lean Transformation at Escorial
read more
outh WalesBluedog Fences Australia views Shinka Management as a trusted partner and a critical component of our journey toward manufacturing excellence.
Shinka Management’s consultancy services, together with their training programs and Lean Japan Tours, have played a key role in embedding a strong culture of continuous improvement within our organisation. Amid recent market volatility, our focus on quality enhancement, cost reduction, and lead-time improvement – driven by their guidance – has enabled us to thrive. Notably, advancements in material flow and our adoption of 5S methodologies have made significant and measurable contributions to our profitability.
The Shinka Management team has actively engaged with personnel at every level of our business, from senior executives to frontline operators. Their consultants leverage extensive practical experience to connect with and inspire our workforce, making lean manufacturing principles accessible and actionable. Moreover, their support is enriched by a wealth of resources, including photos, videos, and case studies originating from Japan and around the globe. These authentic, real-world examples have empowered our team to rethink and improve our manufacturing processes independently, enhancing both morale and operational efficiency.
Such has been the transformation on our shop floor that it now serves as a sales showroom for customers and visitors, reinforcing confidence in our brand and manufacturing capabilities. Bluedog Fences Australia’s substantial progress in our continuous improvement journey would not have been achievable without our valued partnership with Shinka Management.
read more
During 2024, we carried out a project with Shinka that lasted about 5 months, which aimed to improve and perfect our daily management instances, since these had become very time-intensive and with a sense of planning and not performance. After reviewing the current situation and defining our future state, Shinka supported us to refocus our efforts, starting with training and strengthening knowledge, through practical exercises and accompanying us in the creation and updating of our KPIs. Along with that, it helped us to redefine our standard, giving us tools that have allowed us to maintain it and avoid falling into the same previous error, which was mainly not carrying out a constant review of the routine, identifying gaps and correcting them quickly. This has allowed us to hold truly effective meetings, focused on performance and adding value to the organization. I would also like to highlight that Shinka adapted very well to our requirements, understanding our needs and being flexible when it came to modifying the project times, since right during its development, we had an important organizational change and they quickly managed to adapt to the changes and allowed us to adjust the Gantt without major issues.
read more
Thanks to the support of Shinka Management we were able to move forward in the implementation of Lean Manufacturing. More importantly, we took another step towards the cultural change we want to generate in our company. In this way, our employees are increasingly committed and focused on achieving continuous improvement.
read more
Together with Shinka Management, Rieter China reached a new level of lean production capability. Through site workshops and on-site support we could develop our staff with the latest lean methodologies. The direct link between theory and practice was the main driver for the successful development of our lean program here in China. Our Production and Management teams learned a lot from Hyodo Sensei’s extensive production management experience. Thanks to this support we implemented continuous improvement practices in all production departments, including a successful lean office program!
read more
Techdrill recently engaged Shinka Management to conduct a review of our HDD drilling operations daily production. The management team found the presentation and final report extremely useful. This has enabled us to introduce measures to address the inefficiencies thereby increasing productivity.
read more
Our Clients
Contact us about our Lean Consulting Services
Shinka Management supports clients in over 70 countries with lean manufacturing consulting, online lean training and study tour services. Our consultants are based in Japan, USA, South America, Europe and Australia, and travel to support clients internationally.