,
Lean Leadership Master Class | Lean Training | Perth
Western Australian companies have the opportunity to learn from one of the world’s leading lean manufacturing practitioners and trainers. As a Toyota factory manager and kaizen leader, Hyodo Sensei has built a 40 year career as a kaizen sensei fostering the Toyota Production System within Toyota, its supply-chain, and more recently within non-automotive companies.
Date: 28 Aug 2023 - 29 Aug 2023
Time: 8:30 am - 4:00 pm | Timezone: Australia/Perth
Training Location: Affinity Windows, 5 Compass Road, Jandakot, WA 6164
Site Visit: Affinity Windows
Pricing: AUD 1,295 (excluding GST)
For further details of Shinka Management’s training programs, see our lean training page or contact us.
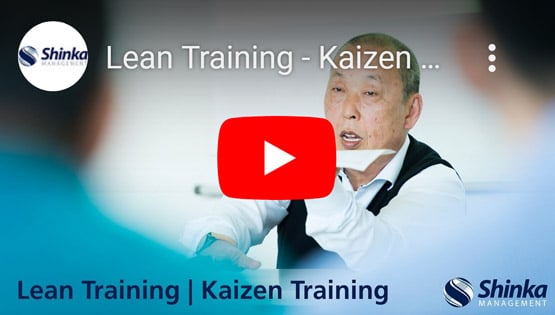
Hyodo Sensei
The master class will be led by Hyodo Sensei, a long-time leader in Toyota Production System training and former factory manager at the Toyota factory in Japan responsible for the manufacture of the HiAce vehicle. Now retired as a factory manager, Hyodo Sensei heads the Toyota Dojo (kaizen training arm) of that Toyota factory providing lean training courses for companies in Toyota’s supply chain and Toyota factory tours, and hosts the training component of the Shinka Management Lean Japan Tour.
Career highlights include:
- Factory Manager Toyota Parts Factory
- Factory Manager at Toyota Assembly Plant
- 13 year member of All-Toyota Kaizen Promotion Team
- 27 years leading TPS at No.1 quality ranked Toyota factory
- Consulting globally serving a wide range of industries
Who is this for?
This master class is designed for Managing Directors and Operations/Production/Continuous Improvement/Quality Managers interested in fostering a culture of continuous improvement within their organisation. You will learn first-hand about how process improvement is achieved within Japan’s leading companies, and more importantly, how to implement these practices within your operations.
Particularly relevant sectors include manufacturing, food and beverage, defence, wholesale & retail trade, and transport.
Topics Covered
This two-day master class will focus on the application of lean principles and the Toyota Production System (TPS) to sectors outside of automotive. The course will go beyond theory to discuss how lean thinking can be implemented and sustained within a company.
- TPS principles
- Developing human assets
- Role of top management
- Factory visit and diagnosis
- Factory visit review
- 5S and visual management
- Standardized work creation
- Continuous improvement culture
The course will also include an overview of the operations at the Toyota HiAce factory in Japan, as well as an afternoon tour and mini diagnosis at a local facility.
What our lean training participants have said…
The training course was very valuable to our organisation. Great results were achieved. I am still using the tools for improvements.
read more
In our experience it is hard to find good quality training. We have been very impressed with the content and presentation of the Lean courses run by Shinka. We felt we got really good value, and came away feeling inspired and that we had the skills to improve our business.
read more
outh WalesBluedog Fences Australia views Shinka Management as a trusted partner and a critical component of our journey toward manufacturing excellence. Shinka Management’s consultancy services, together with their training programs and Lean Japan Tours, have played a key role in embedding a strong culture of continuous improvement within our organisation. Amid recent market volatility, our…
read more
A great training experience with a very wise lean practitioner, simplifying understanding of approaches to lean.
read more
QTEC Fire Services partnered with Shinka Management to implement the 5S system within its operations at its head office in Brisbane. We are confident that the new knowledge and information we received during the three days in-house training will further help to make the company even more efficient and understand this is only the first…
read more
Register today
One of our team will follow up to confirm details and to provide an invoice.